How Can We Help?
Setting up a warehouse
Mapping a warehouse
Once the storage space has been identified, it will need to be optimised for your planned needs. Areas to be included in the storage map are:
Bulk storage area
- This is where the majority of items will be stored – it can be densely organised.
- Items in most regular demand should be closest to the goods receipt/dispatch/picking areas.
Goods receipt area
- Estimate its dimensions per the expected incoming volumes: if you expect to receive items in 20-ton truckloads, make sure your reception area is large enough to store the corresponding volume.
Goods dispatch area
- Estimate its dimensions per the expected outbound volumes: if you expect to dispatch items in 20-ton truckloads, make sure your dispatch area is large enough to store the corresponding volume.
Picking area
- Depends on the dispensing units: if items will be dispatched in a smaller packaging unit than they come in, you will need a picking area (bulk construction items such as nails, bolts or medicine, as you will dispense packs or bottles in smaller quantities than the base carton quantity).
Truck docking area
- For trucks to station and manoeuvre and offload. Include level docking platform if possible.
Office space
- Ensure office space can be isolated from noise and vehicle movements and is ventilated.
- A safe path to the office space must be kept clear at all times.
Packing materials storage area
- Use to store carton boxes, pallets, wrapping and strapping materials.
Cold chain area
- For items which require specific temperature conditions.
- Move close to power supply source and ventilation.
Quarantine area
- For expired, damaged items or items pending inspection or test results.
- Must be lockable.
Sanitary facilities and breakout area
- Ensure respect for cultural norms.
Emergency exits and fire fighting equipment
- Must be signalled clearly.
Security shed/corner
- For security personnel to use during shifts and to store their work equipment. Should be located near the main entrance to the warehouse compound.
A table detailing the different areas is available to download here.
Each of the areas should be clearly separated from one another and space between stacks, racks, shelves or pallets must be included to allow for passage and cleaning.
Depending on how the goods will be handled (manually or with specialised equipment), the space between storage blocks will be different. For human handling, 1.2m is usually enough. Where specialised equipment (forklift, sack truck or hand pallet truck) is used, the manufacturer will be able to confirm the required turning circle.
Each storage unit must be at least 50cm away from the main wall of the warehouse.
Standard layouts include:
U-flow
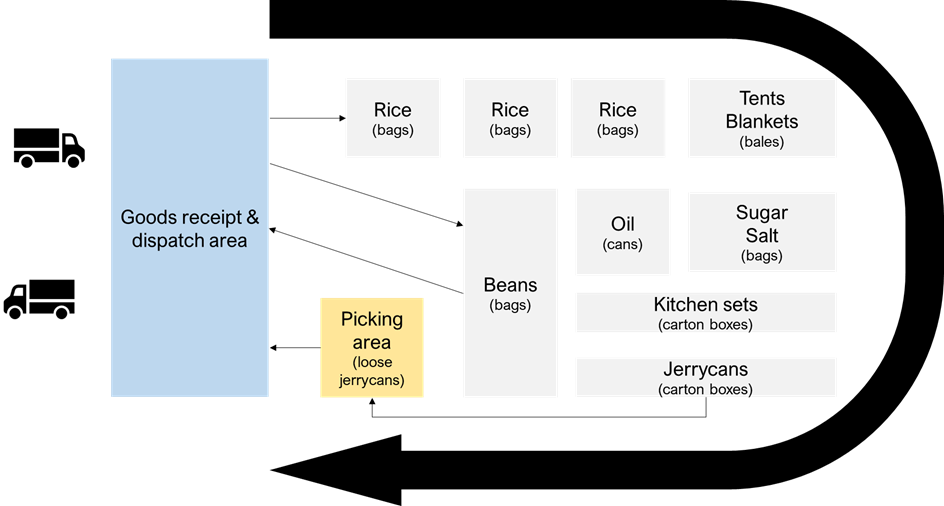
Available to download here.
U-flow is used when the receiving and loading areas are next to each other on the same side of the building. It provides the following features:
- Because the receipt and dispatch areas are side by side, the space can be used flexibly, particularly if these activities are scheduled to take place at different times in the working day. This can save space.
- Personnel and equipment can be used in a flexible way, reducing the overall requirement for resources.
- Because the main access to the building is in one place, access and security are easier to manage.
- The building may be extended on three sides where required and where the site allows.
Through-flow
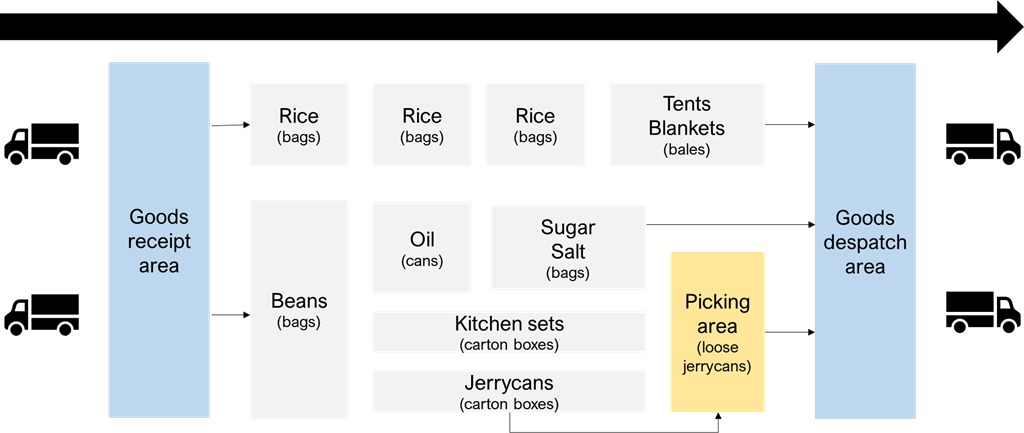
Available to download here.
Through-flow is used when the receiving and dispatch areas are at opposite ends of the building. It tends to be used under the following conditions:
- Where vehicles and equipment used in receipt and dispatch are of different types.
- Where the flow of vehicles around the site will be facilitated (there may be separate gates at opposite ends of the compound for example).
The warehouse manager should ensure that all areas of the warehouse are physically identified, and a map of the warehouse must be available and posted on its walls.
Equipping a warehouse
Depending on the type of goods to be stored, the activities that will take place in the warehouse and the equipment available, the warehouse will have to be fitted with office equipment, specific storage equipment, additional safe storage space and/or partitioning.
In certain cases where the warehousing activities are expected to be critical to the operation and include large volumes of items, it may be relevant to invest in handling equipment.
In all cases, the storage facility will have to be equipped with a fire prevention system.
Storage options
A stack is a pile of the same item on a warehouse shelf.
Goods must be stacked separately and sorted by programme ownership, expiry dates or final destination, for example.
A bin card must be physically attached to each stack or grouping with the same , batch number and expiry date.
Wherever possible, stacks should be placed on pallets and not directly on the floor. Where possible, they should be wrapped in plastic sheeting or tarpaulins.
Where supplies of pallets are limited, note that bagged foods are more vulnerable to humidity than canned or bottled products, so food items should be palletised in priority.
Where pallets are not available at all, items can be temporarily stacked on plastic sheeting laid on the ground.
The distance from stacks to walls and between the stacks must allow a person (or a forklift if using) to pass and be at least 50cm.
The recommended size of a stack is 5 x 5 metres and a maximum 2.5 metres high with bags stacked by 5 x 10 = 50 in each layer x 14–15 layers (= ~ 700 bags).
The stack height will be affected by the type of packaging; boxes and jute bags stack higher than woven polypropylene bags, which tend to slide. When stacking cartons, ensure that lower packages in the stack are neither crushed nor torn. Commodities packaged in tins and plastic bottles, have lower restrictions in terms of maximum stacking heights.
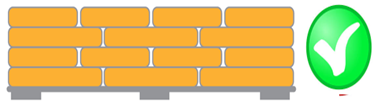
In addition to height restrictions, oil packages frequently indicate a recommended maximum number of rows for stacking. Check the instructions on packaging, where they exist, or consult the suppliers for information.
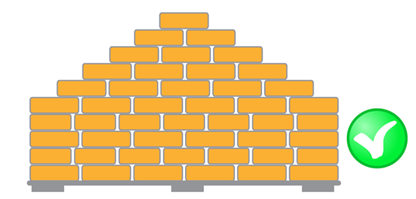
Where stacks are tall, it is useful to tie a rope around the top layer to stabilise them.
Bags that need to be stacked higher than 2.5m should be stacked up to 2.5m as shown here, with the additional layers stacked in a pyramid to avoid slippage. Plastic sheeting can be added between layers to prevent slippage.
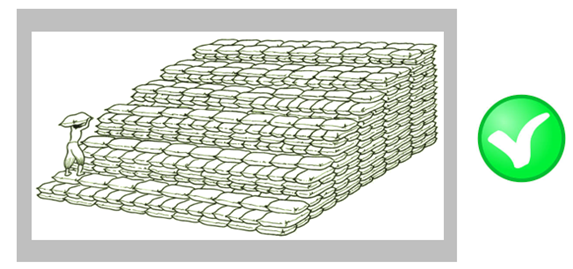
Volumetric storage
Create a one-cubic metre container to measure sand, gravel or a quantity of construction materials in bulk. This works well for timbers, poles, bamboos and items stored in “bundles” of 100 pieces for example.
Pallet racks
Simple pallet racks usually have two or three tiers. Two tiers of pallet-racking require a clear total height of about 3 metres and three tiers require a clear total height of about 4.5 metres. It is possible to have more tiers, but sophisticated mechanical handling equipment is then required.
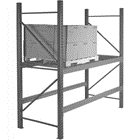
The benefits of shelving and pallet-racking can be combined. The bottom tier of racking may be used to store the working stock if arranged at a convenient height for manual order picking. Alternatively, a special picking shelf can be placed immediately above the bottom tier of pallets. In both cases, the upper tiers can be used to store safety stock or bulk stock. Caution: check the racks’ load-carrying capacity with their owner/manufacturer or an independent engineer before using them and check every rack regularly for signs of damage.
Keep space between the racks and the walls, ensure that the racks are stable and, where possible, fixed together and to the wall and/or to the floor.
Large racks
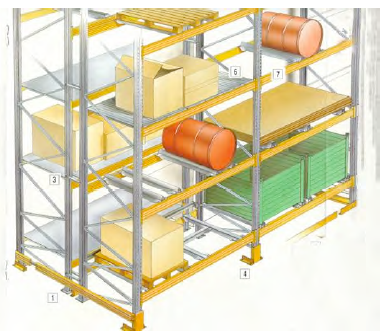
Large racks are useful when storing large inventories of a variety of types, and where the dimensions of pallets are not the standard dimensions of packaging. The racks pictured here have the advantage of adjustable racking height.
Leave space between the racks and the walls.
Ensure that the racks are stable and where possible, fixed together, to the walls and/or to the floor.
Shelves
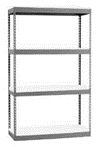
Use shelves where there are a lot of small items and/or when there are items that need repacking or picking (medical supplies, kits, etc). Storage on shelves does not require mechanical handling. In tropical countries where termites attack wood, metal structures are preferred. Shelves can be taken apart and adjusted to suit the goods to be stored.
Keep space between shelves and walls to improve ventilation.
Choosing the best storage options
Bulk items (loose)
- volumetric storage
- 1,000 kg = Variable volume
- volume defined at item level, as item density varies
- 1,522 kg of gravel = 1cbm
- 1,922 kg of sand = 1cbm.
Food in bags (grains. flour, sugar, salt)
- stacked on pallets, with chicken wire between pallet and supplies
- 1,000 kg = 2cbm.
Food in cans or bottles
- stacked on pallets
- 1,000 kg = 1.5 cbm
- ask manufacturer for maximum stacking layers.
NFIs in boxes
- stacks
- adjustable racking
- check stackable height where items are fragile.
NFIs in bags or bales
- stacks (fenced)
- adjustable racking
- 1,000 kg = 8-10cbm
- stacks if stable
- adjustable racking preferred for bales.
Construction materials
- bundles of xx units
- 1,000 kg = Variable volume
- keep stacks fenced with timbers or wiring.
Medical supplies (drugs)
- large racks for main storage
- shelves for picking units.
Medical equipment
- Pallet racks or large racks.
A table detailing the best storage options is available to download here.
In addition to the above, note that to store medical and/or food items you will likely need:
- cold chain equipment: passive (ice packs or other isotherm systems) and active (power-generated)
- a locked storage space for controlled substances
- a quarantine area equipped with shelves/racking.
See the storage of food and medical supplies sections in Managing a warehouse.
Manning your warehouse
Based on the process mapping exercise (part of the stock strategy definition – see the How? section of Stock strategy definition in Building a stock strategy), adequate resourcing will be required for the operation of the warehouse.
The size of the warehouse team will depend on the size of the operation, and the allocation of tasks should be adjusted accordingly (one member of staff may cover several of the below functions). Below is a standard organisation chart including all the skills needed to operate a warehouse.
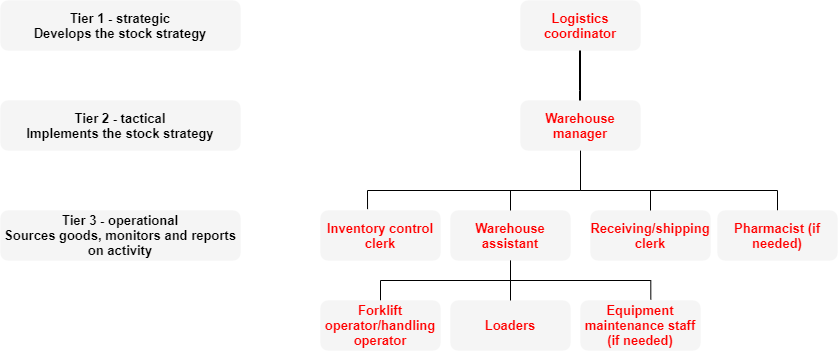
Available to download here.
Recruiting a warehouse team
Standard job descriptions are available on request from the international logistics team.
The
logistics team can provide examples of written tests for recruitment on request, should you need them.Guards and security staff and services can be either hired as staff or day labourers, outsourced as a service or included in the lease of the warehouse. Where guards are hired as staff or day labourers, the warehouse manager will have to define working patterns and shifts (rota). Ideally, these should be captured in a guards’ shift planner.
Some situations will call for a set of core permanent staff, with the arrangement for temporary staff to meet periodic increases in demand or workload. Holding a register of daily workers with contact details and specific skills, managed by the warehouse manager only, can be useful.
Host National Society (HNS) volunteers can also help in the warehouse during periods of high activity, but this must be agreed with the HNS and their procedures and practices must be observed in terms of volunteer hours, incentives and payments. Do not engage volunteers as regular staff without prior approval from and consultation with the HNS.
Advantages | Disadvantages | |
---|---|---|
Hired as staff | Permanent staff with benefits Can be trained and retained | Must manage working hours and performance directly Ensure status in country allows recruitment in own NS's name |
Hired as daily labourers | Flexible workforce Wide pool to recruit from HNS can provide volunteers | High turnover of staff |
Outsourced | Flexible workforce Guaranteed professional service | Limited control over allocated resources - competition with other clients |
Included in warehouse lease | Not included in head count No direct management | Limited control over allocated resources No control over ethical management standards |
Available to download here.
Managing the warehouse team
Warehouse managers are permanent staff members,
staff or volunteers. They are responsible for all activities related to stock movements: the reception, storage, release, dispatch and recordkeeping for all goods.The warehouse manager defines, schedules and coordinates the activities and resources that need to be available to deliver the mission of the warehouse. They also oversee security arrangements, control the recruitment of day labourers and manage the schedules, payment, performance and training of all warehouse personnel.
Regular team meetings should be held, organised by the warehouse manager:
Frequency | Attending | Purpose |
---|---|---|
Monthly | Complete warehouse team and logistics delegate | Monitor performance against set objectives and discuss updates on projects |
Weekly | All warehouse staff | Warehouse manager to present operational objectives of the week and reflect on past week |
Daily | Individual briefs to loaders and receiving/despatching staff | Allocate daily tasks |
Available to download here.
Where daily labourers are regularly recruited, a system must be in place to request the number required each day, record their attendance and report to finance for payment. For example, the receiving/shipping clerk should request through a daily worker request form, signed off by the warehouse manager. Attached to daily worker record sheet, the whole file should be submitted to finance for weekly payment at an agreed time. As far as possible, day labourers should only be hired as security guards, cleaners and loaders.
Read the next section on Managing a warehouse here.
Related resources
Download useful tools and templates