How Can We Help?
Building a stock strategy
Assessing the warehouse requirement (number, location and operation)
During the design phase of a programme, a stock strategy should be developed, including the potential requirements for warehousing. This should fit into the wider supply chain strategy for the programme (see supply chain strategy template and guidelines).
Warehouses are needed when the time required to purchase and mobilise relief items is expected to be lengthy or when responding to a protracted crisis where the risk of disruption to the supply chain is high.
A network of warehouses may also be required to ensure the rapid and efficient delivery of relief supplies. Since most British Red Cross programmes are short-term (a maximum of several years) the need for a new permanent warehouse is rarely justified, although it can be considered as a long-term solution for an
supporting future programmes.Stock strategies must be in line with organisational strategies because holding stock with a projected high value is a risk to the organisation. Other supply chain options, such as the delivery of goods taking place closer to the required time, are sometimes preferable.
Programmes should not be built around the stock strategy (What do we have?) but a stock strategy around the programme (What do we need?).
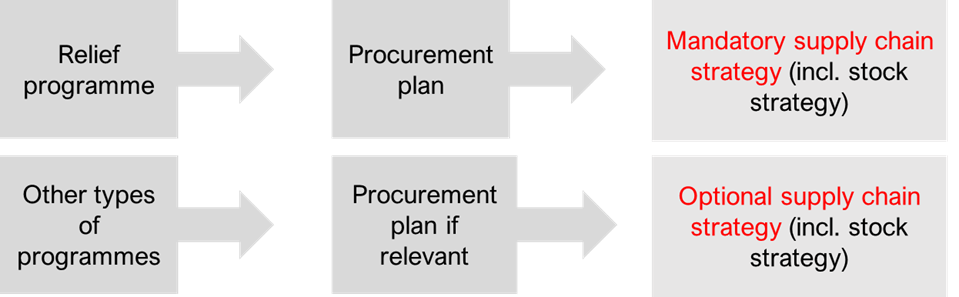
Available to download here.
Quantity and location of warehouse(s)
- type of items to be stored
- scale of operation and required stock levels
- geographic and seasonal conditions
- distances to programme site(s) and supply entry points
- infrastructure available
- availability of transport services
- lack of other storage options (vendor-managed inventory, 3rd party warehousing etc.).
-> Number and location of warehouses required for an operation
Stock strategy definition
View the stock strategy definition diagram here.
During the planning phase, the programme team should provide a range of information to enable logistics to develop a stock strategy.
What?
Storage requirements vary depending on type of items.
Medical supplies and drug shipments can contain small and high value items, many of which have a limited shelf-life.
A secure area is required, and close attention must be paid to expiry dates.
Antibiotics and vaccines require temperature-controlled cold storage arrangements, with sufficient capacity and a reliable power source, with a back-up option.
Combustible items such as alcohol and ether must be stored separately, preferably in a cool, secure shed in the compound and outside the main warehouse.
Non Food Items (NFIs) can usually be stored in bulk with no specific storage or handling limitations.
Dangerous goods such as fuels, compressed gases, insecticides and other flammable, toxic or corrosive substances, are hazardous.
International regulations require specific markings to identify their dangers.
Consider the volumes to be stored: the quantity to be stored and the frequency and size of deliveries and dispatches will influence the stock strategy definition.
Consider whether the stock strategy will involve holding and handling kits in stock. If so, how much kitting activity is expected to take place in the warehouse? Kits are often used in emergencies, when the aim is to provide large quantities of a standard set of items to large numbers of people.
The IFRC standard product catalogue (SPC) includes a wide variety of kits, normally provided as full kits by long-term suppliers sourced by the .
Detailed information on handling hazardous substances can be found here.
Detailed information on managing kits can be found here.
Where?
Where is the programme being implemented and where are the goods required?
Think about:
The geographical location (is access by road, sea or air?)
Is it a rural or urban area?
The number and location of sites
The security situation
What warehouses are available, in the region and country, in and outside of the Movement, and what are their associated costs?
What are the options and costs of renting commercial warehousing?
What are the options and costs of using temporary Rubb Halls (mobile storage units, or MSUs) or containers (a last resort, due to cost, storage conditions and their difficulty to manage)?
-> Gathering this information will allow for a decision on where along the supply chain to position the warehousing (at global, regional, local or field level).
Consider the option and cost of having vendor-controlled inventory (VCI). Where there are long-term relationships with suppliers, suppliers can hold stock for the
in their own warehouses. The stock is prepaid by the RCRC and released with a simple stock request. In this case, requirements need to be carefully calculated and transport costs closely estimated as they are likely to be higher. A VCI strategy is viable where the variety of items required is small and can be supplied by a maximum of two or three suppliers, who are willing to collaborate and consolidate shipments to control transport costs.When?
A detailed timeline (start and finish dates for the programme), with requirements scheduled throughout the programme’s implementation will help (this can usually be inferred from a good procurement plan).
Details of the frequency of deliveries and dispatches will also be helpful here, as well as estimations of the time needed to fulfil the ordering cycle. It is advised to estimate the average throughput of the warehouse in order to support the dimensioning of the required storage space (how large will orders in and out be on average helps define the dimensions required for reception and despatch areas for example).
Try to define durations for standard warehouse processes such as:
- time from delivery at warehouse to storage location in warehouse (dock to shelf IN)
- time from receipt of requisition to availability to dispatch (shelf to dock OUT)
- stock takes cycles and associated warehouse closures.
How?
Design the reception, requesting, dispatch and reporting processes at an early stage of the programme design, to inform the level of human, financial and administrative resources required.
Questions to ask when defining a warehouse resourcing strategy:
- How will deliveries be managed?
- Who will process them and how will they be documented?
- How will requests from users be managed?
- When will they be received by the warehouse team and how will they be documented?
- Who will prepare the orders – in what timeframe, at what frequency, with deliveries done where – at the warehouse door or at the site?
- How will dispatch operations be managed?
Who will oversee the booking of transport and how will transport be booked?
How will dispatch be documented, who will validate dispatch and how will delivery rounds be organised? - How will stock reporting be compiled and communicated?
What information will be recorded and what will the reporting cycle be – weekly, bi-monthly or monthly?
How much?
The setting of minimum stock levels must be discussed between the logistics and programme teams.
The logistics team should make a recommendation based on the programme’s requirements, to be assessed by the programme team in view of objectives, budgets and timeline.
Factors to consider when setting a stock minimum:
- total population in area
- total population at risk in case of disaster
- types of disasters that may occur
- probability of disasters occurring
- type of items needed
- replenishment time = time taken to get relief items from HQ or other partners in the area
- response capacity of the branch – number of active volunteers trained in emergency response and/or logistics
- available storage space
- available transport.
There are a set of criteria that support defining the ideal inventory level. Usually these include:
The budget available for warehousing and transportation costs. Limited resources will influence what type of warehouse activities the programme can afford, in terms of storage space, transportation possibilities and human resources.
Clarifying the different purposes of the inventory. See table:
Working stock | Safety stock | Preparedness stock | |
---|---|---|---|
Purpose | To meet normal or expected demand for humanitarian goods between deliveries. | To mitigate the risk of stock-outs in the period between deliveries (due to increased demand or decreased supply). | To meet sudden increases in demand. |
Depends on | Level of demand Order frequency Vehicle spare parts, fuel | Unpredictability of demand Unpredictability of supply Risk appetite | Organisational policy Availability of funds and resources to manage Household items |
Available to download here.
Understanding the stock-time curve: this is about managing the supply and demand. The usage rate of stock can vary and it is important to identify and record times when the safety stock is used. See the below diagram that illustrates the stock-time curve.
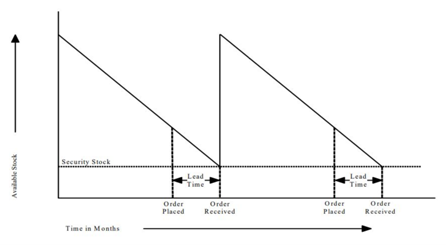
Available to download here.
Using forecasts: estimating demand and supply capacity will support the accurate definition of order quantity and frequency. Forecasts will be based on the organisation’s strategy (how they define preparedness requirements in the stock strategy paper), assessment reports (how they define working stock levels in assessment reports) and short-term forecasts and risk assessments (how they define safety stock levels in the programme plan).
Choosing an ordering system: choose the trigger for placing a replenishment order. Apart from the stock level and the usage rate, two factors can determine what is the right time to place an order:
Order placement and delivery lead time
Order quantity
Considering the shelf life of items held in stock in the ordering cycle.
To determine the order frequency and quantity, the free stock level is the most important information to have at hand.
Physical stock on hand
+stock on order from suppliers
+stock in transit
-reserved stock
=Free stock level
Reserved stock is stock already allocated to orders in preparation, or stock otherwise reserved for special purposes.
There are two different “standard” re-ordering systems:
Two-bin system:
- This is best used for low-value items.
- Stock is kept in two separate bins (50 per cent in each).
- When Bin One is empty, start taking from Bin Two and replenish quantity for both.
Periodic review system:
- Replenish system options:
- Top-up system – at each review, place an order to top up from available stock to a target stock (agreed with stock owners).
- Minimum stock system – place order when free stock is less than minimum stock (a “re-order point”).
Bear in mind that other factors can impact the order quantity, such as the minimum order quantity set by suppliers or the available budget.
Remember
Reorder quantity (ROQ) = average daily usage x average delivery lead time
Reorder point (ROP) = ROQ + safety stock
When ROP is reached, an order should be placed to the ROQ quantity calculated.
Safety stock must be an organisational decision (expressed in days’, weeks’ and months’ usage), based on risk appetite.
ROQ should be calculated with daily, weekly and monthly numbers consistently across the calculation. This calculation takes consumption during both the order lead time and consumption in general into account but variations (higher or lower consumptions) will not be incorporated.
A concrete example:
The initial situation:
In the Sinapai branch, they decided to stock at least 50 family kits (=50 lanterns, 50 buckets, 50 jerry cans, 150 blankets…)
Their actual stock is 60 complete family kits.
The distribution:
After a small disaster, the branch distributed 10 family kits with 15 extra jerry cans and 10 extra blankets.
The new situation:
They only have 35 complete family kits left.
Replenishment needs:
They absolutely need to replenish 15 jerry cans and 10 blankets to reach their stock minimum of 50 complete family kits.
General considerations for stock strategy definition
- Are there other programmes planned (by British Red Cross or another ) with similar activities that could potentially fit into one stock strategy? If yes, ensure strategies are aligned and well embedded.
- If stock strategy poses too high a risk or does not provide , can alternative modalities be considered? Think of vendor-controlled inventory, or stock managed by partners.
- Are there any previous experiences with this or context we can draw from? Consult with other programme managers.
- How does the stock strategy support development of the capacities of the HNS? How is it aligned with its strategic objectives?
- Logistics can advise ordering extra items for safety, but this must always be agreed with the budget holder (or programme manager) before placing the order.
Estimating your storage space needs
Once it is confirmed that one or several warehouses will be needed to deliver the objectives of the programme and with the storage location(s) agreed, you will need to estimate the storage needs.
The size and type of the warehouse will depend on the required storage capacity for an operation and is determined by the maximum quantity (in tonnage and volume) of supplies to be stored.
This may be different from the total quantity required for the whole operation. The quantity of stock to be held and the number of warehouses to use will vary along the duration of the programme and is determined by the programme plan.
The required storage volume depends on the weight-per-volume ratio of the goods. The area occupied in the warehouse by one item depends on its volume, the height of the storage space and the maximum permissible load-per-square-metre of floor space.
To illustrate how volumes can vary dramatically, below are some examples of the average volume in cubic metres (CBM) of one metric ton (MT) of the following items:
Items | 1 MT (1 metric ton = 1000kg) |
---|---|
Grain, flour, sugar (bagged) | 2m³ |
Medicines (Average for bulk shipments and medical kits | 3m³ |
Vegetable oil (in drums or tins) | 1.5-2m³ |
Blankets in pressed bales (approx 700) | 4-5m³ |
Blankets in unpressed bales | 8-10m³ |
Clothes (in bales) | 7-10m³ |
Tents (approx 25 family tents) | 4-5m³ |
Kitchen utensils (in 35-40kg boxes) | 4.5m³ |
When calculating storage requirements, only 70 per cent of the total warehouse’s surface capacity should be considered as available for storage space. The remaining 30 per cent is used to ensure proper ventilation, passageways, handling space and repackaging areas.
Warehouse storage capacity:
Approximate storage capacity of the warehouse = Length x width x (height – 1m) x 70%
How to calculate the required storage capacity:
Add the total weight and total volume of the items to be stored and use the volumetric info from the above table (CBM per MT requirements)
Divide the total CBM by 70 and multiply by 100 to calculate the total warehouse volume needed. Assume 2m stacking capacity. Include truck docking areas (in addition to the storage spaces).
View and download a table demonstrating the calculation of required storage capacity here.
Estimating your floor-load capacity needs
No more weight than that specified in the warehouse leasing contract should be stacked per square metre of floor space. The permissible load at ground-floor level will normally be 1,000–3,000kg/m2, but on upper floors (or ground floors where there is a crawlspace or basement) it can be as low as 500–800kg/m2.
Always do a physical check of the floors – when floors are damaged, their capacity will be reduced.
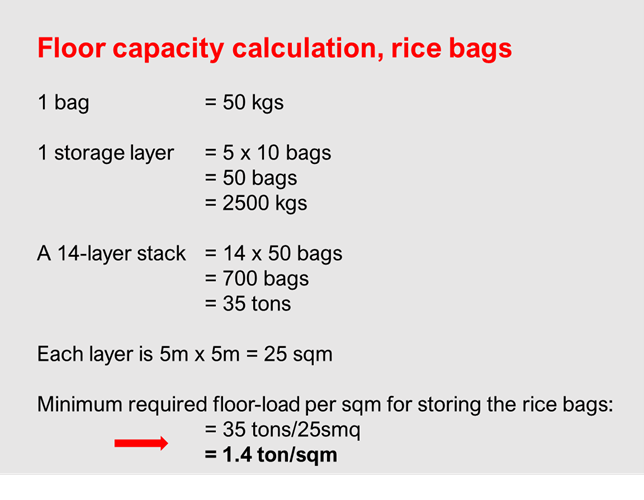
Calculating stock turnover and adjusting target stocks
It is good practice to periodically review the target levels of stock that have been set for a programme and set a stock turnover target (per item and per period) to ensure that the stock targets remain relevant to the operation.
The stock turnover target can vary from one item to another and depends on the context of the operation. At the British Red Cross, the stock turnover target on
stocks pre-positioned for emergency response is equal or greater than two per year: to consider stocks of a specific item as relevant, the ratio of items issued out to the average inventory level in the year must be greater than two.A basic way to calculate the average inventory is the beginning-of-year inventory plus the end-of-year inventory, divided by two:
average inventory = (inventory at beginning of year) + (inventory at end of year) ÷ 2
stock turnover ratio (per item) = total quantity of stock issued out (1 year) ÷ average inventory (1 year)
A few questions to guide the stock review to adjust target stocks:
- Of the total stock, how much has been used (requested or issued stock divided by total stock, in percent) over the period observed?
- What is the total percentage of stock loss (expired, damaged, and lost stock divided by total stock, in per cent)?
- What is the ratio of used storage area vs available storage area in the warehouse?
- What are the objectives of the programme the stock serves?
- What are the relationships of the with established suppliers in the area? Could they provide or respond to needs within a maximum of 48 hours?
Read the next section on Sourcing a warehouse here.
Related resources
Download useful tools and templates
Download the full section here.