How Can We Help?
Stock takes and reconciliation
Inventories (stock takes) are helpful to:
- know what is in stock, by quantity, value and quality
- agree corrective actions in case of discrepancies or poor quality of stock
- update reporting tools.
Stock takes should follow two separate patterns:
Cycle counting
It is good practice to have five per cent of stock, or a minimum of ten stock cards, checked each month.
This process should be led by the warehouse manager or team, with a stock spot check report prepared and shared with the finance team member in charge of stock and balances, and with the stock owner.
All differences must be recorded on the stock spot check report and investigated and explained within one month or before the next stock spot check takes place. This should be done by the warehouse manager, under the supervision of the logistics delegate.
All boxes/pallets that are counted can be sealed and strapped after the finance and programme business partner have accepted the spot check, so they don’t need to be counted again during the 100 per cent stock takes.
Cycle counting can also be done on a predetermined cyclical schedule. Effective cycle counting requires the counting of a pre-set number of items every workday and should result in the counting of all warehouse stock twice a month (refer to the below section on cycle counting procedure).
Cycle counting procedure
The number of stock cards determines the frequency of the cycle count.
To calculate the number of items to be counted daily in order to permit a complete count of all warehouse stock twice during the month, multiply the number of stock cards by two and divide the result by the number of workdays in the month.
For example:
30 stock cards in warehouse: 30 x 2 = 60
20 workdays in month: 60/20 = 3
In this example, the items listed on three stock cards are to be counted each day.
A schedule for conducting cycle counts is then established and integrated into the daily or weekly routine. Bin cards, stock cards and the documents certifying receipt or dispatch (waybills,
) of the supplies being controlled are verified.The latest global stock report is crosschecked against the stock cards. A physical count is performed for the selected items and crosschecked with the stock cards and bin cards. When variances are found, the cause (e.g., count error, recording error, unrecorded dispatch, theft) is identified and appropriate corrective actions are taken.
100 per cent stock audit
It is mandatory to conduct at least one 100 per cent stock take each year.
It is good practice to conduct two 100 per cent stock takes per calendar year.
All counted quantities should be reported on a stock take report, with all discrepancies recorded and investigated, and the report approved by relevant authority (usually head of logistics or head of delegation) and shared with all stock owners and the head of logistics or delegation within one month of the stock take.
Before a stock take:
Stock spot check (monthly) | 100% stock check (twice yearly) |
|
---|---|---|
-90 days | Invite finance and programme business partners to join the count Inform all stakeholders about service interruption |
|
-30 days | Inform stock owner of items to be counted and the date of the stock spot check Ask for no movement of these items on selected date (provide 'last order' deadline) | Confirm counters' attendance |
-15 days | Ensure all orders for items included in the next spot check are in and ready for preparation - they must be delivered before the stock take date | Remind stock owners of warehouse closure Prepare stock take brief Prepare the counting document |
-5 days | Prepare the counting document | Update stock report with latest stock movements Prepare stationary items needed for stock take |
-1 day | Update stock report with latest stock movements of counted items | Ensure all units of same items are stored together (group same items together) |
Available to download here.
During a stock take:
Stock spot check (monthly) | 100% stock check (twice yearly) |
---|---|
Locate items to be counted | Ensure no order preparation is pending Update stock reports with latest stock movements if necessary |
Record a physical count on the stock take sheet (theoretical stock not included) | Brief counters on their role Allocate counting responsibilities |
Mark up all counted boxes (colour code or date-stamp) | Distribute counting sheets Theoretical stock should not be visible on stock take sheet Blank lines should be added to record additional items if needed |
Reconcile physical count with stock cards Highlight and investigate discrepancies Use GRNs, donation certificates, waybills and stock request forms | Ensure counters open every box they are asked to count unless contents of a box have been counted during a stock spot check |
Fill out a stock spot check report and submit to warehouse manager and stock owner | Ensure all counting sheets are handed to warehouse manager and signed off by counters |
Available to download here.
After a stock take
Stock spot check (monthly) | 100% stock check (twice yearly) |
|
---|---|---|
Same day | Record physical count on stock card (report in red or other identifiable format) | Invite finance and programme business partners to join the count Inform all stakeholders about service interruption |
Within 1 week | Update stock report with confirmed physical quantities Seal and strap counted boxes/pallets Agree required corrective actions and record in stock spot check report File stock spot check report | Reconcile physical count with stock cards Highlight and investigate discrepancies Use GRNs, donation certificates, waybills and stock request forms |
Within 2 weeks | Agree required corrective actions and record in stock take report Prepare stock take report, submit to head of logistics and stock owners File stock take report |
Available to download here.
Note: stock audits can be conducted by internal or external auditors, outside of scheduled stock takes. The warehouse manager will have to produce the necessary documents to conduct a four-way match between physical stock, stock cards, stock report and
/waybill/donation certificates/ .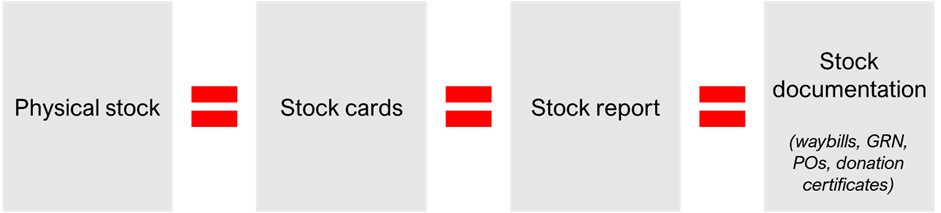
Stock reporting
The stock report
The summary of all stock cards is the stock report or stock movement report, which is used for reporting and overall stock management.
The stock report should be in a simple format, capturing the opening balance, quantities received (split between purchases and donations) or issued (split between requests, losses, donations or disposal), and closing balance for each item in stock.
Stock reports are usually updated on a monthly basis and shared with stock owners as a snapshot of the available quantities in the warehouse, though finance and
-based logistics coordinators may also request to receive them. In emergency operations, this report can be required to be shared on a weekly or a daily basis.In addition to the above, the periodic stock report should ideally highlight:
- the 20 per cent fastest-moving goods in the warehouse
- the 20 per cent slowest-moving goods in the warehouse
- where items are perishable, those quantities expiring within the next six an three months must be highlighted and actions to avoid wastage agreed.
Annexes to the stock report
- The monthly warehouse checklist must be completed and attached to the stock report.
- Quarantined items must either be reported against separately or visually identifiable in the report, with the reason for placing the items in quarantine clearly.
- A warehouse dashboard can be put together and shared with stock owners and other clients to give a measure of the activity level in the warehouse and inform of any upcoming changes (such as deep cleans, training events or stock counts).
- The value of any stock donations (received or issued) must be known by the warehouse team and included in the report for Finance to record. If requested, donation certificates must be produced.
- Ideally, the total value of stock losses (due to expiry, theft or damage) must be known and included in the report for finance to record. If requested, disposal or loss certificates must be produced.
Always consult with the stock owner to be informed of any specific donor requirements. Donors will usually want to know the value and content of the stock balance at the end of a project they fund.
Read the next section on disposing of and writing off stock here.
Related resources
Download useful tools and templates