How Can We Help?
Definitions and concepts
The 11 major rules of running a warehouse:
- Rotate stock so old goods are used first: FIFO (first in, first out). If goods have an expiry date, use FEFO (first expired, first out).
- Stack goods safely.
- Plan the layout of goods for easy access and finding them again.
- Record all movements or losses on the correct forms.
- File all papers immediately.
- Plan ahead: what goods, staff and transport will be required in the next day, week or month?
- Keep goods secure.
- Keep warehouse clean, with daily, weekly and monthly cleaning.
- Dispose of spoiled goods correctly and quickly.
- Communicate objectives, plans, progress and issues effectively.
- Conduct physical inventory on a regular basis.
Definition:
A warehouse is defined as a planned space for the storage and handling of goods and materials. Goods and materials stored in a warehouse are considered as stock, which is also called “inventory”. Warehouses are an integral part of the supply chain, their main purpose being to serve as physical transit points between supply (delivery from suppliers) and demand (end-users or beneficiaries).
Where needed, warehouses allow for the breakdown of bulk deliveries across different requestors or into phased deliveries, and for the combination of loose items into kits to meet beneficiaries’ needs.
A well-managed and well-positioned warehouse allows for speedy responses to both planned and unplanned needs and ensures that both inventory and staff are ready to respond to planned and unplanned needs.
Functions of a warehouse
View and download a detailed diagram of warehouse functions here.
Different types of inventory
It is important to be aware of the difference between stock (inventory), office supplies, office equipment and assets:
Stock | Office supplies | Equipment | Assets | |
---|---|---|---|---|
Definition | Consumable items that are tracked and stored until use or distribution | Temporary or disposable consumables, food or cleaning products required on a day-to-day basis, for use in the office or residence | £1,000 or > 3 years useful life or Powered by electricity or Incurs running costs or Defined as asset by donor | |
Examples | Programme supplies for direct distribution Office supplies for distribution to beneficiaries, partners Vehicle spare parts, fuel | Stationary Office cleaning materials Food for office consumption | Furniture Housing equipment Household items | Owned property Vehicles Comms equipment IT hardware Large household appliances |
Reporting requirements | Stock report | None | Property register | Asset register |
Storage location | Warehouse | In the office | In use or in storeroom* | In use or in storeroom* |
*The storeroom is typically a small room in the office where a small stock of office supplies is kept
Available to download here.
Purposes of holding stock
The main purpose of stock is to de-couple supply and demand in an operation that requires the provision of pre-determined goods and materials.
In an ideal world:
- exact needs are known
- suppliers are reliable
- supply is stable
- infrastructure is stable
- there is little to no need for inventory.
In the humanitarian world:
- needs fluctuate unpredictably
- suppliers are liable to multiple risks (environmental, political, financial)
- supply is often interrupted
- infrastructure is exposed to multiple risks (environmental, political, financial)
- inventory acts as a buffer against structural risks.
Stock ownership
Generally, stock is owned by its original requestor (the person who pays for the goods) and physical management of items and materials is delegated to logistics.
This means that logistics cannot choose to increase or decrease stocks unilaterally and that updates on inventory must be shared between the logistics team and the owners of the stock managed in the delegation.
In that sense, logistics is responsible for the inventory it holds for others, but requestors and programme managers are accountable for the type and quantity of items they require logistics to hold in stock for their use.
Stocks management – roles and responsibilities
RACI matrices are used throughout this manual. They break a process into steps, specifying who is Responsible, Accountable, Consulted and Informed at each step of the process.
Responsible | Accountable | Consulted | Informed | |
---|---|---|---|---|
Warehousing & Stock Management | Warehouse staff | Requestor Budget holder | Programme team Health and safety | Logistics team Finance team |
Available to download here.
The valuation of inventory is critical for the organisation to manage the risk of ownership of stock in general, and in particular to support the definition of insurance requirements.
Financial management of stocks
For financial management of stock in the UK, refer to the Bulwick warehouse SOP, ERU kit SOP, UKO stock management SOP, RLU stock management SOP and the Balance sheet guidance note.
More information on the Regional Logistic Unit (RLU) and Emergency Response Unit (ERU) stocks management can also be found in the RLU stocks and ERUs chapters of the Manual.
The general concepts to bear in mind are:
- Inventory held by international logistics for preparedness purposes is valued in collaboration with the logistics finance business partner, based on procurement information shared by the logistics team.
- The value of inventory held by logistics sits on the British Red Cross balance sheet from the moment stock is received to the moment it is dispatched for use.
- When stock is dispatched for use, the value of the dispatched items is charged to its requestor and taken off the British Red Cross balance sheet.
- When stock needs to be disposed of, logistics must use a write-off form to record the disposal. The value of the disposed items is usually charged to the logistics budget and taken off the British Red Cross balance sheet.
See the Disposing of and writing off stocks and Writing off obsolete assets sections for more details on stock write-offs.
Note: it is recommended that the members of the logistics team who manage stock regularly meet with both their requestors and the finance team to review current stock type, levels and locations, discuss proposed changes (if any), ensure budget management and reconcile stock. In the British Red Cross, the logistics team meet with owners of the stock they manage (ERU kits, RLU representatives) and with their finance business partner on a regular basis.
Stock positioning
Within the Red Cross Movement, stocks are held at different levels and the processes to follow to access stock vary between levels of storage:
Country level
- This is stock that is available in country.
- Locally available stock can belong to the country’s or to a partner NS and would include the kits that a chooses to hold for -led responses.
- NS that do not hold ERUs may also have stocks available in country, either for ongoing programmes or for preparedness purposes.
Regional level
- This is stock that is held in regional hubs.
- In RLUs (Kuala Lumpur in Asia, Panama City in Americas), stocked by the IFRC and other PNSs and managed by the IFRC.
- In sub-regional warehouses or in decentralised regional stores (“cluster warehouses”), in Harare, Douala and Dakar.
Global level
- This is stock that is held in IFRC-managed global hubs.
- The Dubai and Las Palmas logistics centres are “global hubs”, serving all regions equally.
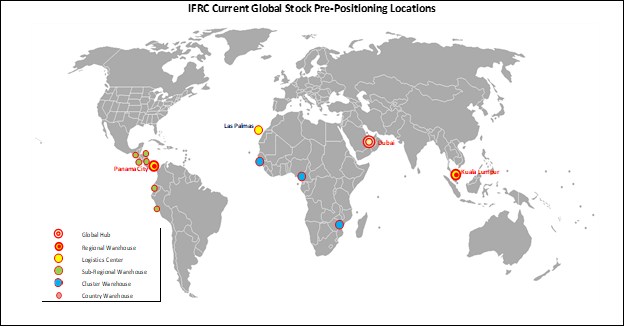
The IFRC’s global stock strategy aims are:
To cover the initial needs of the immediate aftermath of any disaster, the IFRC, with the stock pre-positioning of their members in the different RLU, has pre-positioned emergency response stockpiles in their network of regional warehouses across the globe, which could support up to 450,000 people at anytime and anywhere.
Read the next section on Building a stock strategy here.
Related resources
Download useful tools and templates