Vehicle registration process
All vehicles must be registered in their country of operation, in compliance with local law.
Vehicles (and larger generators) must be registered and insured before they can be considered operational. The registration process depends on the circumstances in which the vehicle arrives in the operation:
- The vehicle is imported new, with no previous registration records.
- The vehicle comes with export plates from the country of dispatch (which may or may not be the country of origin). Export plates usually have limited validity.
- The vehicle is still fully registered in the country of dispatch.
- The vehicle is already deregistered in the country of dispatch.
- The vehicle is registered in a third country.
Import procedures must usually be completed and the vehicle must be customs cleared before it can be registered. In addition to the customs clearance certificate, the below documents will be required:
- invoice
- packing list
- certificate of origin
- vehicle gift certificate (if applicable).
Only a partner with legal status in the country of operation can register a vehicle in their name. Therefore, vehicles used in an operation will usually be registered under the name of the
or the , unless collaborating have legal status in the country of operation.Note: generators and handling equipment do not usually require registration but this can vary between countries.
Insurance
Only a partner with legal status in country of operation can subscribe to an insurance policy. Therefore, vehicles used in an operation will usually be insured under the name of the
or the , unless collaborating have legal status in the country of operation.Vehicles rented through the the IFRC vehicle rental programme) will be included in the IFRC global insurance policy, but additional insurance policies must be subscribed to locally, as applicable (these are usually third-party, theft and accident).
(see the section onRefer to the VRP agreement for more details on insurance claims and payable excesses.
A Federation operation may register vehicles for insurance on behalf of a PNS under the following conditions:
- A fixed asset registration form is submitted and IFRC operation obtains approval from global fleet base.
- The PNS signs an integration agreement with the operation.
- The PNS agrees to respect the IFRC’s standard operating procedure, as laid out in the IFRC fleet manual.
- All PNS drivers are tested and sign the operation’s driving rules and regulations.
- Only drivers with a valid authorisation issued by the head of the IFRC operation may drive the vehicles.
Note: vehicles owned by a PNS and registered under the IFRC are subsequently covered by all IFRC insurance policies.
Tracking vehicle and generator use
For accountability and safety purposes, the use of fleet in an operation must be monitored. It is recommended that regular training is conducted, with refresher training for fleet users and spot checks on the correct use of logbooks.
Vehicle logbooks
Every vehicle operated by the British Red Cross, including rented vehicles, must have an allocated vehicle logbook to monitor the use of the vehicle, refuelling and maintenance.
Every movement of the vehicle must be captured in the logbook, which is an auditable document.
Every entry in the logbook must be signed by the driver (for refuelling), the passenger (for trips) or the fleet manager (for maintenance services).
Where vehicle costs are charged to specific cost codes or programmes, these must be recorded in the logbook, with the passenger or cargo details.
Note: when cargo is transported, reference must be made in the logbook to the waybill associated with the load transported.
Generator and handling equipment logbooks
The use of generators and other handling equipment such as forklifts must also be monitored and auditable. Running hours must be captured in a logbook. Details to be included in the generator and handling equipment logbook include:
- every period of usage (running hours) – signed off by the user in charge
- refuelling – signed off by the person in charge
- maintenance services – signed off by the fleet manager or mechanic (as applicable).
The generator (or equipment) handbook must be controlled by the logistics lead at regular, pre-agreed intervals. The logistics lead should sign or initial pages after each regular check.
Generators and handling equipment should normally be allocated to a specific cost code or programme. Where that is not the case, details of the recharge must be indicated on the logbook.
Safety and security
General vehicle safety
Fleet procedures and road safety policies are in place to ensure maximum security for drivers, passengers, and vehicles, and must be adhered to.
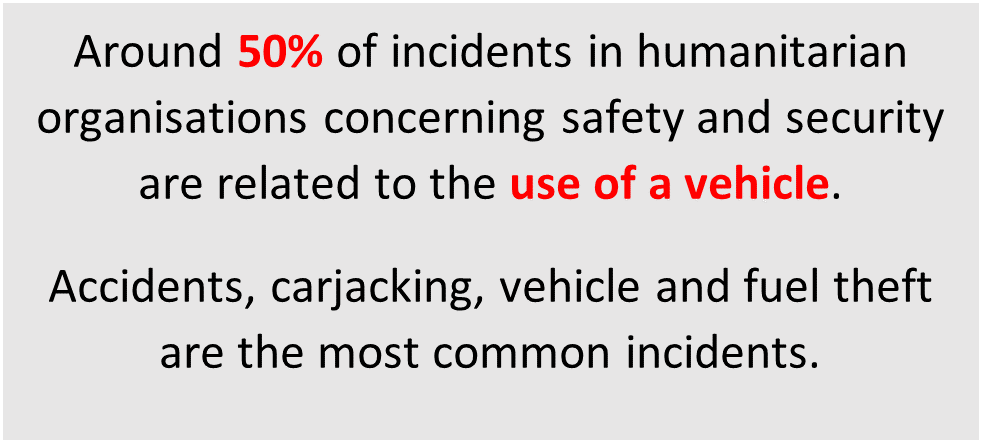
All vehicles must be mechanically sound and roadworthy. Fuel, tyres (including the spare), water, coolant, brake fluid, steering fluid and oil levels must be checked regularly.
Refuelling should be optimised so that a vehicle’s tank is always at least half full.
Depending on context, all vehicles should be equipped with communication equipment, emergency repair materials (spare tyres, jump leads, vehicle jacks), passenger safety equipment (safety belt, drinking water), accident preparedness equipment (first aid kit, fire extinguisher, list of contact numbers). All vehicles must be equipped with Red Cross markings, including emblem and no weapons sign.
As per the Asset maintenance section, inspection and maintenance must be planned, conducted, and documented, in order to ensure that vehicles and generators are safe and efficient.
The driver of a vehicle is responsible for checking the condition of their vehicle and all necessary equipment in the vehicle, while the facilities manager is responsible for checking the condition of generators.
View a list of elements that make up a good driver here.
Using generators safely
Where generators are used as back-up power or a primary power supply system, the below recommendations will ensure safe usage of the units.
Generator sheds (see the example design below) are recommended to limit access to the generator and protect humans and animals. It also ensures that only one person oversees the maintenance of the generator.

- Distance between the top of generator and the ceiling is a minimum of 1.5 metres to ensure good ventilation and access for maintenance. Around one metre is required around the generators and between two generators.
- There is a well-secured area with a lockable gate, blocked from weeds growing in but sufficiently open to let gas escape.
- There are enough openings in the structure to allow good ventilation, both at the bottom and the top.
- There is sufficient space for the storage of oil, funnels etc. Fuel should not be stored in the generator room/shed.
- There is an exhaust outside the structure, protected from rain and a straight pipe without sharp angles.
- There is firefighting equipment – an ABC-type fire extinguisher and a bucket of sand with a shovel as a minimum.
Generator safety basics:
Set-up
- Ensure the ground (or preferably the concrete foundation) is strong enough to hold the weight of the generator.
- Elevate the generator by 10–20cm above the ground to prevent it from flooding.
- In very hot conditions, generators might overheat. A running schedule should be used to allow the generator to cool down. Do not open the doors of the generators while it is running, as this disables the cooling function.
Usage
- Do not daisy chain extension cables, as they will melt.
- Do not overload the generator by connecting too many appliances at the same time. See appliances’ kVa rates table in the Power supply section.
- Make sure a grounding pin is properly installed to the generator, and that all the cables and appliances have a connection with grounding.
ICRC convoy procedures
When operating in the field, the
and other Movement partners often travel in convoys. Because of the nature of ICRC operations, unarmed and in conflict situations, humanitarian personnel often travel in a group of vehicles, for protection purposes. The head of delegation decides in what situations this is necessary.The aim of the ICRC Convoy Procedure document is to provide guidelines to staff organising or joining convoys. The list of responsibilities is designed to help conveyors and drivers in the field, before, during and after a convoy.
British Red Cross driving procedure
The British Red Cross has a Driving in the British Red Cross policy that must be adhered to when driving a British Red Cross vehicle in the UK.
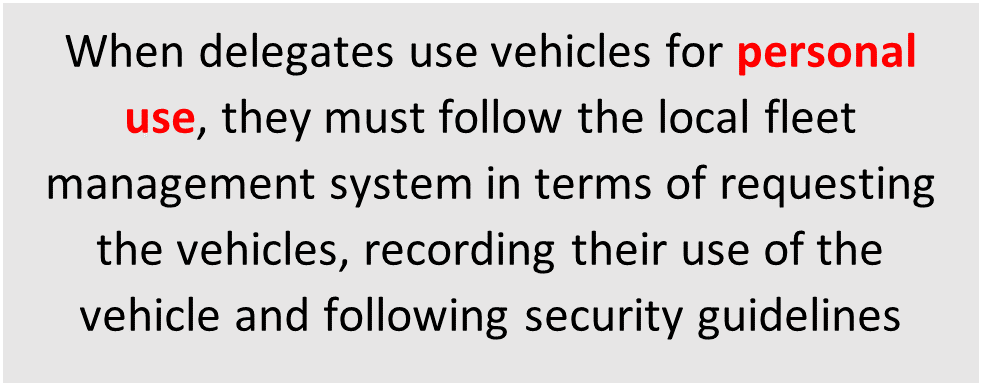
When driving a British Red Cross vehicle outside the UK, the agency with security lead (the
, or ) provides driver regulations. It is the responsibility of every British Red Cross delegate to enquire about applicable driver regulations when joining a Red Cross operation.Provided that they have passed the driving test and hold an official driving license, delegates may be allowed to use vehicles for personal use. However, rules applying to the personal use of vehicles will vary depending on the context of the operation, and advice should be sought from the IFRC or the HNS.
In some operations, the personal use of fuel will be recharged to delegates.
Note: logbooks must be kept up to date for personal as well as professional use.
IFRC driver rules and regulations
All personnel deployed within the driver rules and regulations form before they are authorised to drive a Federation vehicle.
must read and sign a copy of the operation’sThe form sets out both country-specific rules and standard operating procedure for the use of Federation vehicles. A signed copy of the form will be kept in the staff member’s personnel file.
The default position on IFRC and other Red Cross missions is that delegates are not allowed to drive themselves, unless the country-specific driver rules and regulations allow it. Medical evacuations and security situations are treated as exceptions to that position.
The standard driver rules and regulations form must be adjusted to reflect country-specific conditions. The head of operation for a Federation operation, the head of project for a
operation or the secretary general for a National Society operation determines the country-specific rules concerning vehicle use (for example, conditions for and limitations on delegate driving, mission order procedures, country-specific security regulations, etc).The fleet manager or delegated authority must ensure that all vehicle users are aware of Federation procedures and country-specific rules, as well as local driving regulations and conditions.
All drivers, including delegates, must have a valid driver authorisation form, signed by the head of operation and the fleet manager, before they are permitted to drive a Federation vehicle. The authorisation must specify the types of vehicles permitted and any limitations on their use.
Note: passengers are restricted to National Society personnel (volunteers and staff), IFRC and
staff. Members of UN agencies and other NGOs are permitted as passengers, as long as travel is within the scope of the Movement’s activities. Transporting other passengers or cargo is not allowed, except with previous authorisation from the IFRC country representative or staff in charge of managing local security (for example, programme manager, ops lead, etc).All drivers, including delegates, must undertake a test of driving ability in their country of station or deployment.
British Red Cross safety training pathway
Refer to the Safety training pathway section in the Warehousing chapter.
Planning for usage
A well-sized fleet should aim for maximum usage, with minimum “idle” time and maximum availability for requests, with minimum service interruption or “down-time”.
Requesting a vehicle and cost recharge
To ensure vehicles are consistently available and sufficient for an operation’s needs, with a minimum number of vehicles underused, a request system that is as simple as possible and as complex as necessary will be helpful.
There are multiple ways in which users can request vehicles:
Vehicle whiteboard – used on a daily basis, listing all available vehicles. Requestors write their name and department on the whiteboard, with trip details (destination, departure time, number of passengers, estimated duration).
Vehicle requests should ideally be recorded at the end of the week for the next week, with an agreed level of flexibility for unforeseen circumstances.
Vehicle request form – submitted to the fleet manager or dispatcher within an agreed timeframe before the vehicle is needed.
Cargo transport request form – for the transportation of goods within an authorised area.
If the transport request is to locations outside of the authorised area, it should be accompanied by a mission order.
These methods are applicable to cases where vehicles are needed for local movements on a single day. Longer trips outside of the operating area or multiple-day trips must typically be approved through a field trip form or mission order, which requires sign-off from line manager, fleet manager and potentially the security manager (depending on context).
Vehicles are usually managed as a pool by the logistics department. Other departments can request to use vehicles, usually on a daily basis, and their usage can be recharged to the requestor through the pool management system.
Vehicles can also be fully allocated to a specific budget, with all costs related to them, including driver, fuel, maintenance and insurance, charged to that budget.
Note: logistics usually has budget to cover fleet maintenance costs, but unusual maintenance services can be charged to requesting departments as applicable.
Fleet productivity: utilisation and performance
In order to review the size of the fleet, monitor usage and report on fleet performance, it is recommended to track productivity in different dimensions.
Fleet performance can be measured looking at:
- Utilisation – resource used (number of vehicles used over period) divided by the available resource (total number of vehicles available over the period). Expressed as a percentage:
No. of vehicles used over the period ÷ total no. of vehicles available over the period = fleet utilisation as a percentage.
- Performance – actual tonnage (or passengers) moved divided by total tonnage (or passenger space) available in a period. Expressed as a percentage:
Tons transported over the period ÷ total tons available to transport over the period= fleet performance as a percentage.
Vehicles’ performance can be measured looking at:
- Utilisation – number of days/hours used divided by the total number of days/hours in a period. Expressed as a percentage:
No. of days or hours vehicles was used over the period ÷ total number of hours or days in the period = vehicle utilisation as a percentage.
- Performance – number of days available for used/total number of days in a period. Expressed as a percentage:
No. of days in the period that the vehicle was available ÷ total no. of days in the period = vehicle performance as a percentage.
Note: where the vehicle’s performance is <80 per cent, the vehicle is not performing well enough and should either be replaced or given a revision.
- Downtime: days that a given vehicle is not available for operations, due to planned or unplanned maintenance (ideally the split between planned and unplanned should be detailed).
Where no logistics staff are available, country representatives/delegates should seek support from
, or logistics coordinators to compile the fleet performance data.For more details on reporting for fleet, see the Reporting on fleet section.
Read the next section on Managing fleet here.
Related resources
Download useful tools and templates here
Download the full section here.
Whenever vehicles are used to transport goods belonging to the Red Cross Movement, it is strictly forbidden to transport:
- weapons of any sort
- any personal items or other freight not directly related to the operation requiring transport services
- people, be they Red Cross personnel, military, or beneficiaries. An exception would be providing urgent transport to the nearest medical facility, but this must, as far as possible, be agreed with a security or fleet manager beforehand and captured in an incident report upon return.
Any observed breach of these rules must be immediately reported in an incident report.
Reporting incidents
All incidents involving British Red Cross staff or property must be reported – refer to the British Red Cross or applicable National Society’s incident reporting procedure for information on how to do this.
Where British Red Cross delegates are seconded into another organisation such as the
or , or where they are working under the umbrella of another organisation such as a , this organisation’s incident reporting procedure must also be followed, in parallel to that of British Red Cross.Use of military transport means
As per the Movement guidelines on the use of military and civil defense assets (MCDA) in disaster relief:
“Military assets should only be used as a last resort, where there is no civilian alternative and only the use of military assets can meet a critical humanitarian need.”
No armed escort is allowed for shipments undertaken for the Red Cross Movement, unless:
- There is extremely pressing need (e.g., to save lives on a large scale).
- It represents no added security risk to beneficiaries.
- No one else can meet the needs.
- Armed protection is for deterrence and not firepower.
- Parties controlling the territory are in full agreement with armed escort.
- Protection against bandits/criminals is needed.
- Authorisation is given in advance, at the specified level – typically secretary general or senior director within the HNS and ICRC/IFRC in Geneva.
All military actors run the risk of not being perceived as neutral and jeopardising the Red Cross Movement’s commitment to neutrality and impartiality. Absolute rules in terms of using military resources are:
- Never use armed military transports.
- Never use the assets of a party involved in an armed conflict.
- Never use military assets simply because they are available.
Use of the RC emblem on transport not owned by Red Cross
Red Cross-owned fleet will always bear a Red Cross emblem. The decision on which emblem (
, , British Red Cross or ) to use will be made in discussion with the lead Red Cross Movement partner and the HNS – this applies to both Red Cross-owned and Red Cross-rented vehicles.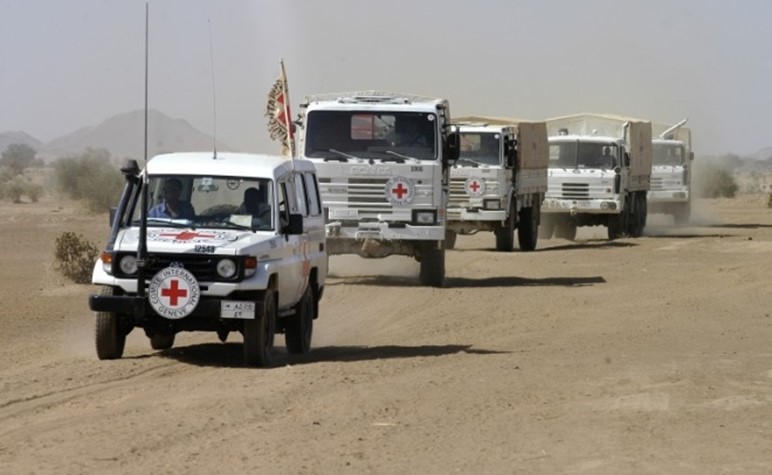
Where fleet is rented, the emblem must be clearly visible on the rented vehicle (truck, small vehicle, boat, or plane).
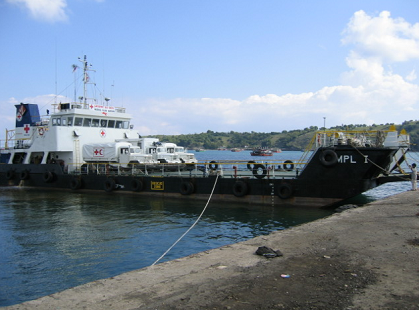
On road vehicles, flags should be used at the front of the vehicle. The emblem, in whatever form, must be removed and retained by the Red Cross logistics or transport manager immediately after the vehicle is no longer serving the Movement.
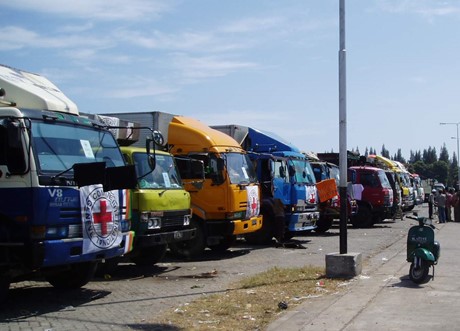
Based on the above conditions, where the Red Cross agree to use military assets for transportation, vehicles must visibly carry the emblem.
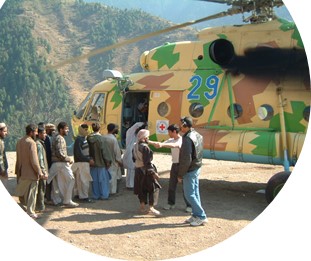
Read the next section on Transport documentation here.
Related resources
Download useful tools and templates here
Download full section here.
In a warehouse there is the potential for serious incidents or accidents to occur.
Every effort should be made to reduce the risk of accidents:
Equipment:
- All equipment (e.g., trolleys, sack trucks and hand-operated pallet trucks) should be carefully and regularly maintained.
Specialised equipment must only be used by trained, authorised employees (some equipment may require load testing to ensure they are fit to use). - Access in areas where forklift trucks are used should be restricted to prevent people being hit during loading and unloading activities.
Storage:
- Racking and shelving should be regularly checked.
- Shelving with collapsing stacks should be immediately restacked.
- Shelving and racking should be firmly secured to the floor or to the building – if this is not possible, keep racking to only two levels.
Facilities:
- Toilet facilities and welfare areas should be provided, so that breaks can be taken away from the main warehouse.
Personal safety:
- Staff must be issued with protective clothing where required (based on an assessment of risk) – specifically, boots and gloves for handling heavy and bulky goods.
These must be kept clean and regularly inspected to ensure they are fit for purpose and replaced when they are not.
A record of PPE equipment must be kept on site. - Ensure all staff are aware of hazards and are fully trained in safe working techniques, including manual handling techniques.
- First aid kits should be available and regularly checked, and one or more permanent warehouse staff should be trained in basic first aid.
Hazards:
- All hazardous materials like oils, lubricants and fuels should be assessed so the correct action can be taken if staff are exposed to a spillage.
All materials will have a safety data sheet which provides this detail and is available from the manufacturer. Safety data sheet are supplied for all the materials in storage. - Immediately clean up spilt goods, especially oils, lubricants and fuels, as this will reduce the risk of slips and falls, as well as the risk of fire.
- Expired goods and food items no longer fit for human consumption must be correctly disposed of immediately.
Check with local health authorities to determine whether they can be used as animal feed or for the appropriate disposal method: incineration or burial. - Smoking is prohibited in the warehouse and adjoining compound.
- Cooking and open fires should be restricted to designated areas in the compound – never inside the warehouse.
- Damaged pallets should either be repaired or discarded.
Guidelines for the manual handling of heavy loads
- Assess the weight of the item and ask for help if it is too heavy for you to lift safely.
- Clear a path and know where you are going.
- Lift with your legs and knees.
- Hold the object close to your body with your feet a shoulder-width apart.
- Keep your eyes up and your back straight. Avoid twisting, as this places extra strain on the back.
When undertaking a site risk assessment, contact the local health and safety focal point. This will usually be the
in multilateral operations, but it can also be coordinated by the or the . For warehouses in the UK, the focal contact person is the Health and Safety adviser, who must inspect all buildings used and rented by the British Red Cross.Fire safety in the warehouse
Warehouse staff must be trained as fire wardens – see the Safety training pathway section below.
For UK warehouse-staff, contact the health and safety team to receive fire warden training (a three-hour, face-to-face course).
Find detailed information on fire safety in the warehouse here.
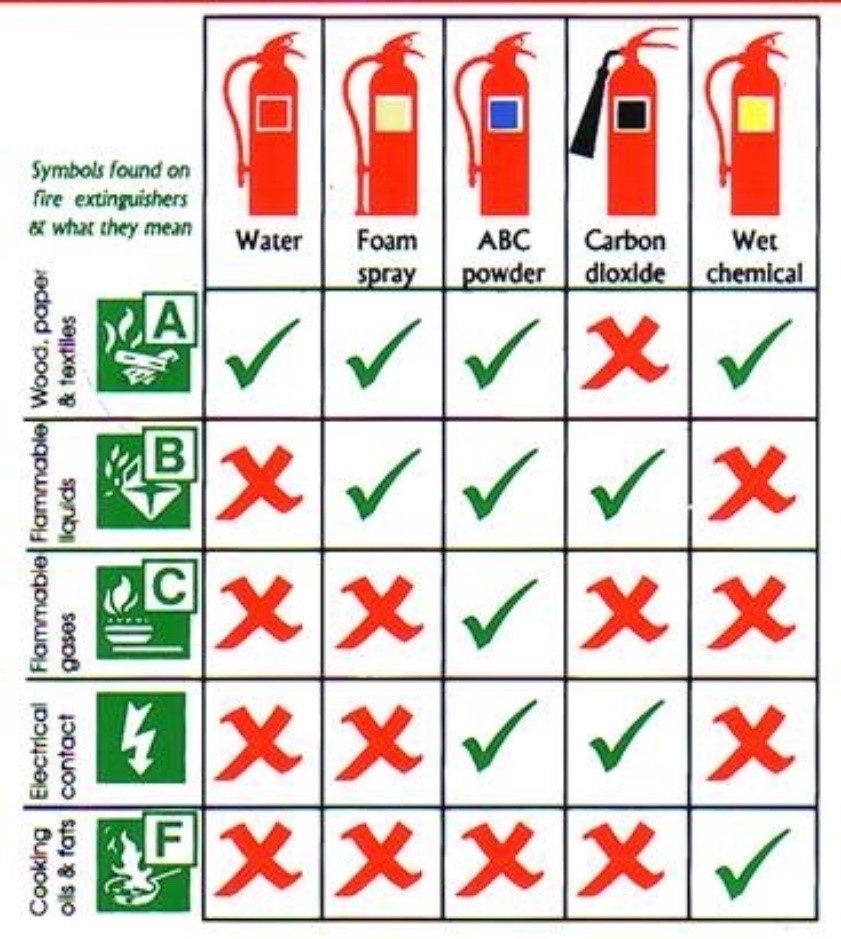
Different types of fire extinguishers can be identified by a coloured band:
- red for water
- cream for foam
- blue for dry powder
- black for carbon dioxide.
Wet chemical extinguishers are not widely used in the Movement – fire blankets are available for cooking areas.
Examples of useful fire signage:
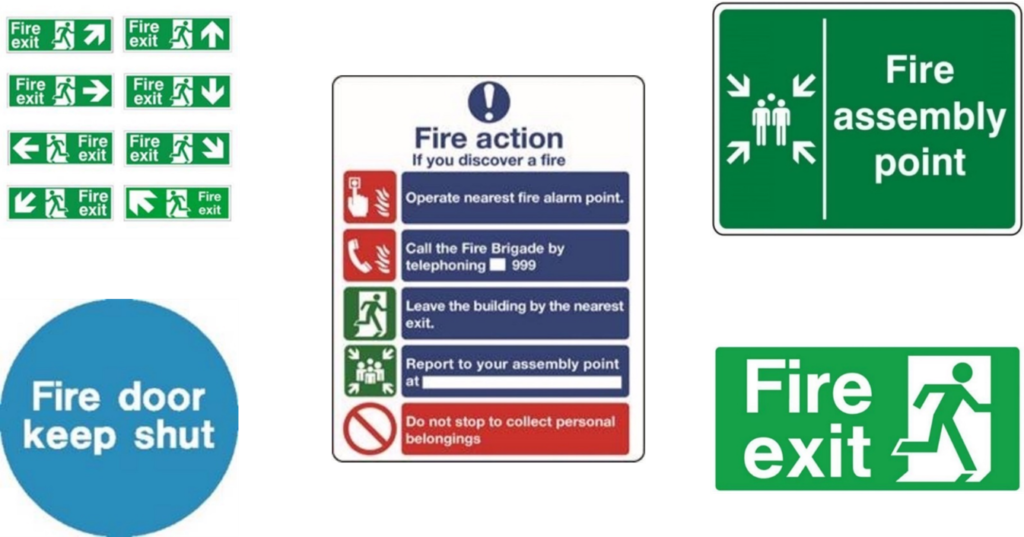
Available to download here.
Managing dangerous goods
See the Storing dangerous goods section of Managing a warehouse for details on handling dangerous goods.
There are different regulations in place for different modes of transport and in every country.
Ultimately, for all modes of transport – sea, air, rail, road and inland waterways – the United Nations Committee of Experts on the Transport of Dangerous Goods and other organisations, which includes the International Air Transport Association, have assigned dangerous or hazardous substances one of nine classes, in order to help make the transportation of dangerous goods as safe as possible.
Note that the number of the class of dangerous goods does not indicate the degree of danger.
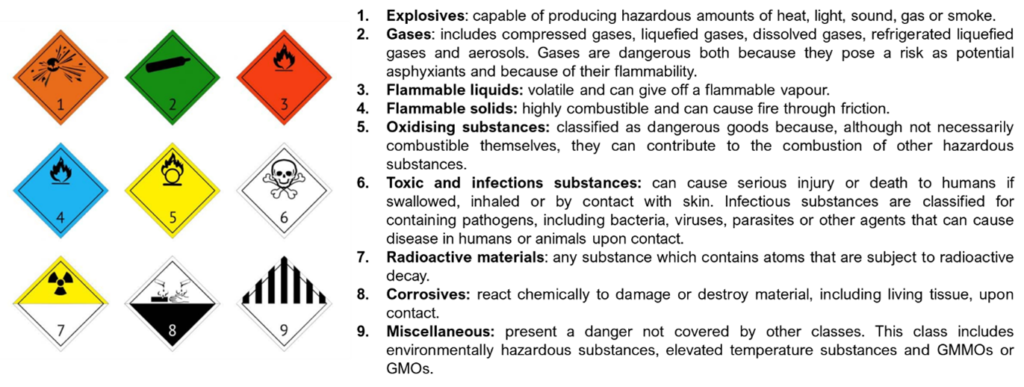
Dangerous goods require specific documentation and handling methods: packing, moving and transporting them is highly regulated and should be overseen by a third-party service provider.
Safety training pathway
The British Red Cross employs a full-time health and safety advisor to facilitate a variety of training, most of which is bespoke. Below is a list of the most common training delivered, most of which can be delivered remotely. The health and safety team are working on collating a standard catalogue of the available training; in the meantime, feel free to contact them directly.
The below training courses address safety from an occupational safety perspective and not from a personal security perspective, which is addressed in the
courses developed and managed by the security team based in . The below falls under the delegate refresher requirement and must be refreshed every two years.Content | Target audience | |
---|---|---|
Driver safety training | Vehicle, traffic and driver safety awareness training | All drivers of RC vehicles |
General safety awareness training | Occupational health and safety (basics) | All staff with roles that involve manual handling of goods |
Risk assessment and management training | How to identify, mitigate and report risks | All managers of staff working in environments where manual handling takes place |
Hazardous substances training | How to identify and manage hazardous substances | All staff with roles that involve the manual handling of potentially hazardous goods |
Warehouse safety management training | Racking, shelving and handling goods | All warehouse staff |
Environmental protection training | Managing the risks of warehouse activities on the environment | All warehouse staff |
Available to download here.
Read the next chapter on Transport here.
Related resources
Download useful tools and templates