Sourcing fuel and maintenance services (in-house or outsourcing)
Sourcing fuel
The way fuel is purchased for operations will vary widely. In certain contexts, it is widely available through standard commercial services such as filling stations, but in other contexts it is less widely available and is distributed through local traders and networks.
Procurement of fuel
Like any other commodity or service, fuel must be purchased following the applicable procurement, fraud and corruption and counter-terrorism policies. However, due to the importance of fuel to the success of the operation, it usually requires more control than the procurement of other items or services after it is purchased. Both the quantity and the quality of the available fuel must be monitored closely.
Where possible, at least one contract should be in place to ensure the supply of fuel – multiple contracts will mitigate the risk of shortage.
The contract(s) should detail the expected quality of the fuel provided, and supplied fuel should be checked regularly against agreed quality standards (by an independent laboratory if necessary).
Where contracted suppliers cannot supply fuel, alternative options can be explored, in which case the purchase must follow the applicable procurement policy. For example, where a supplier has been contracted but is facing a one-week shortage, the fuel for that week must be purchased through the applicable procurement process, determined by the cost of the estimated total amount required for the week.
Fuel suppliers’ performance must be closely managed, and periodic contract reviews are recommended due to the criticality of fuel availability.
Fuel purchasing cards
In urban contexts, fuel purchasing cards are widely available. These cards are usually connected to an online platform, through which the fleet manager can track consumption.
Fuel cards can be pre- or post-paid, and they allow drivers to refill vehicles without having to request cash. Fuel refills must still be recorded in the logbook, and receipts must be kept for traceability and reconciliation purposes.
Fuel purchase vouchers
Where filling stations cannot provide purchasing cards, the fuel purchase vouchers.
recommends the use ofEach vehicle should have a purchase voucher booklet in which drivers can record fuel purchases. Each voucher must have a unique number, which should be recorded by the fleet manager.
The fuel purchase vouchers must be signed by the driver, the filling station attendant and the fleet manager, with copies kept by all parties.
At the end of the month (or of a pre-defined period), the filling station can issue an invoice against all fuel purchase vouchers in the period. The fleet manager must then reconcile the vouchers against his own records (including the vehicle logbooks).
Fuel deliveries to point of use
In other contexts, fuel may need to be delivered periodically to one or several operating sites.
In this case, the delivery site must ensure that storage facilities are available to safely stock and issue fuel (an isolated, locked storage area only for fuel, equipped with fire extinguishers and sandbags, permanently staffed and with ideally only one staff member issuing and reporting on fuel distribution, and proper fuel issuing equipment).
Having the right refuelling system, with fuel vouchers and proper approval scheme in place under the supervision of the fleet manager, is critical in this context, to ensure consistent consumption control see the Daily checks on vehicles and generators section.
Where fuel is delivered directly from a supplier, they should provide a set of documents including certificate of quality, certificate of origin (especially if fuel is imported) and delivery note.
Fuel should be sampled and tested, ideally on site. Fuel testing does not require sophisticated equipment; a used fuel filter and a tube of Kolor Kut water finding paste are often enough to detect dirty or water-cut fuel. Kolor Kut paste should be smeared on a dipping stick, which is then plunged into the fuel container for two seconds. If the colour of the paste changes, the fuel contains water. Other brands of water-finding paste work in similar ways.
Sourcing maintenance services
Depending on the context of the operation, maintenance services can be provided in different ways. Each presents advantages and risks:
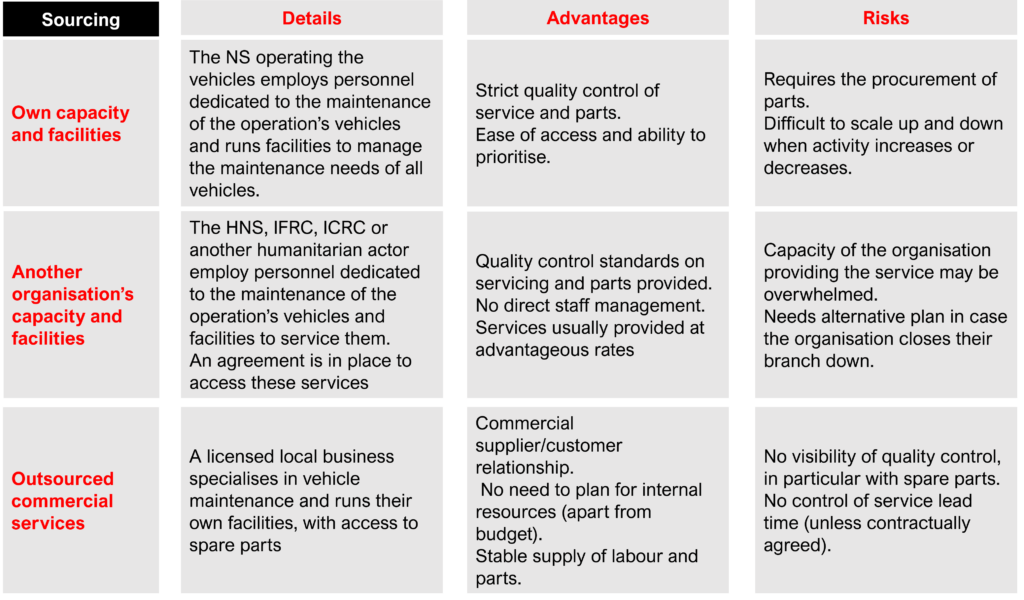
Available to download here.
Where maintenance services are outsourced, they should be sourced through the appropriate procurement process. Ideally, a contract or framework agreement should be in place with at least one service provider, detailing a service level agreement and performance management principles.
Vehicle and driver schedules, generator running hours
Vehicle and driver schedules
Office hours drivers must work in accordance with local legislation regarding working hours and length of duty. Drivers should ideally be assigned to a single vehicle, to ensure traceability and accountability of resources.
In locations where no personal or public means of transportation are available, a duty driver system can be implemented to provide transport services outside of working hours, within a designated area. This ensures that delegates have means of transportation outside working hours.
Duty drivers should remain on standby for designated shifts in evenings and at weekends.
recommends:- Minimum of four drivers available (each covering a six-hour shift, for 24-hour availability – consider security procedure for evacuation in specific contexts.
- Minimum of one vehicle available for each duty driver.
- Means of communication must be available for the duty vehicle/driver (either a VHF handset or mobile phone, depending on local phone coverage).
Duty driver allocation should be based on a rotation system and in line with local labour law.
Generator running hours
Just as logbooks track usage of vehicles, a generator’s running hours must be monitored, to ensure regular maintenance and follow-up regarding consumption.
A generator logbook should be available for each generator in use, tracking the number of hours it is used, maintenance services and refuelling (time, date and litres).
In operations that rely on generators to provide more than 50 per cent of the electricity requirements, it is recommended that the use of generators is alternated either with batteries (which can be charged by the generator when in use) or with spare generators, to limit wear and tear, allow for rest periods and guarantee back-up in case of servicing or breakdown.
Daily checks on vehicles and generators
Daily checks on vehicles
With all vehicles, it is usually the responsibility of the driver to carry out the necessary checks. Ideally, a daily inspection checklist should be available for the driver to fill out, but verbal follow-up or a note on the vehicle logbook can be sufficient in smaller operations.
The minimum daily inspection should be based on the FLOWER technique:
F – Fuel: fuel level must be checked.
L – Lights: all lights to be checked.
O – Oil: check oil level when engine is still cold and vehicle is parked on a flat surface.
W – Water: check the coolant level and top it up with coolant or water if level is low. Do not mix anti-freezes. Check the screen wash reservoir.
E – Electrics: check the battery is safe and secured in its place.
R – Rubber: check tyre pressure (finding the recommended pressure either in the vehicle manual or on the frame of the driver’s door), uneven wear, side wall damage and tread depth (check the tread indicator on the tyres).
A FLOWER diagram is available to download here. A more detailed vehicle inspection checklist is available to view and download here.
Daily inspections on generators
Like vehicles, generators should be inspected daily and any defects should be flagged as early as possible.
View and download a generator inspection checklist here.
Following fuel consumption
Taking stock of fuel
As the volume of fuel fluctuates depending on ambient temperature, the use of metric tons (MT) is recommended as the unit of measure for ordering, receiving and taking stock of fuel (fuel issued can be recorded in litres but quantities should be included in metric tons for stock taking).
To avoid discrepancies, use a calibrated, non-metallic dipstick.
For fuel stock takes, a temperature correction of fuel volume calculation table exists to advise how to adjust the fuel quantity according to temperature.
Where the fuel is managed by the organisation at the operation’s level, fuel stock reconciliation must be made across fuel requests, vehicle logbooks, fuel deliveries and by a physical count. Where fuel is purchased directly from filling stations, no stock take is required, but invoices must be reconciled against logbooks and receipts.
Monitoring fuel consumption
A variety of tools is available to monitor fuel consumption:
- where fuel cards are in use, reports can be provided by the supplier
- fuel request vouchers
- logbooks
- fleetWave system (where available).
To calculate fuel consumption, use the below formulas:
For vehicles:
Consumption = litres consumed ÷ distance covered (km) x 100 = XXX litres per 100 km
For generators:
Consumption = litres consumed ÷ hours operated = XXX litres per hour
Generally accepted consumption rates can be found here.
-based logistics coordinators or regional fleet managers can support the analysis of variances if needed.Maintenance planning and tracking
Ensuring the proper maintenance of fleet reduces the risk of accidents, and of damage or loss of goods handled by logistics and delays to the delivery of items.
The importance of preventative maintenance
Preventative maintenance encompasses all actions taken to prevent vehicle failure. Regular maintenance where vehicle and generator parts are lubricated, adjusted, tightened, or otherwise checked will prevent most of the common mechanical failures. Preventative maintenance guarantees staff safety, while also saving time and money.
Benefits of preventative maintenance:
- Vehicle condition is under control and any misuse is flagged at an early stage, avoiding damage to the vehicle.
- All deficiencies in the vehicle condition can be corrected at an early stage.
- Adjustments and repairs can be carried out easily.
- Time needed for repairs is shorter.
- Costs of repairs are lower.
- Need for major repairs is less frequent.
- There will be fewer unforeseen breakdowns of the vehicle/generator.
- The equipment’s lifecycle will be lengthened.
Planned maintenance
The fleet delegate or manager must ensure that all vehicles and equipment are maintained and serviced according to instructions in their user manuals.
All vehicles should carry and maintain up-to-date records of maintenance, including a maintenance schedule. Drivers or other users of fleet must inform the fleet manager of planned maintenance on the equipment they are responsible for.
The
fleet management system allows the tracking of maintenance history and planning. Where FleetWave is not in use, this information can be kept in the vehicle file or on a vehicle follow-up spreadsheet.Service schedule
Below is an indicative table of recommended maintenance milestones. Local regulations may require a stricter maintenance schedule and it is not uncommon for governments to require maintenance records to be kept on file for a number of years.
Type | Maintenance milestones |
---|---|
Light vehicles | Every 5,000km (10,000km maximum) or 18 months |
Heavy goods vehicles | Every 15,000km or 18 months |
Motorcycles | Every 10,000km or 12 months |
Handling equipment | Every 250 hours |
Generators | Maintenance (including oil and filter change) every 100 hours |
Engine oil should be replaced every 10,000km, depending on the quality of lubricants in use.
Unplanned maintenance
Planned maintenance should ensure that unplanned maintenance is required as rarely as possible. However, where a malfunction is reported by a driver or other vehicle user, usually following usage or a daily check, unplanned maintenance may sometimes be required immediately, leaving the vehicle unavailable for the duration of the service.
Defects or malfunctions should be reported through a maintenance request form, signed off by the requestor, the fleet manager and the budget holder (usually the logistics delegate or programme manager) and logged in the vehicle file or on a follow-up spreadsheet.
Where no logistics staff are available, country representatives/delegates should seek support from
/ or logistics coordinators to advise on maintenance requests and cost recharges.Incident reporting
All incidents involving British red Cross staff must be reported – refer to the British Red Cross incident reporting procedure for further information.
Where delegates are seconded into another organisation such as the
or the , or where they are working under another organisation such as a , this organisation’s incident reporting procedure must be followed in parallel to that of the British Red Cross.Reporting on fleet
Managing and reporting on fleet performance is an important component of operations management. Where it is in use, FleetWave can produce monthly performance reports, but this requires disciplined submission of source data. For more information about using FleetWave, contact the
-based logistics team or the global logistics services team in Dubai.For information on calculating basic fleet performance, see Fleet productivity: utilisation and performance and Monitoring fuel consumption sections.
Other important indicators of fleet performance may include:
- environmental impact measurement
- total cost of ownership
- benchmarking against other fleet options ( , rentals, etc.).
The Fleet Forum has developed performance-measuring tools that cover these indicators, among others. The group has also proposed a fleet management reporting format, which supports monthly data collection and analysis.
Fleet performance can be reported as part of the logistics monthly report, or separately where the fleet size is more than 30 vehicles and where a fleet manager oversees a dedicated fleet department or team.
Read the next section on Fleet disposal options here.
Related resources
Download useful tools and templates here