How Can We Help?
Releasing stock
Remember to apply the First In, First Out rule: all supplies should, in principle, leave the warehouse in the order in which they arrived. The exception is the First Expired, First Out rule; items with expiry dates must be distributed according to their expiry date. Additionally, damaged, infested or damp goods that are still fit for human consumption must be repackaged and distributed before older stocks and without delay, to avoid further loss.
Remember that management of the stock is delegated to the warehouse manager or Logistics delegate in charge of the warehouse, while ownership of the stock remains with the budget holder, generally the programme manager. Therefore, logistics must guarantee the traceability of stock movement and report to the stock owner on the same.
To support this, systems must be implemented to release stock, deliver items safely and document all stock requests processed by the warehouse team.
Prior to releasing stock from the warehouse:
Stock release must be authorised by the stock owner.
Generally, requisition forms are used as stock request forms to document approval of the stock release, by ticking the “request for stock issue” box. Where this option is not available, a separate stock release form should be developed.
The stock request form should be filled out by the requestor, reviewed by the requestor’s supervisor and approved by the stock owner. The warehouse team should also sign the stock request to signify their acceptance of the order preparation task. The warehouse team is responsible for keeping the approved stock request forms on file and must be able to give access to the records during an audit.
A packing list must be raised and communicated to both the requestor and the consignee of the stock (if different). It must provide a breakdown of the consignment per packaging unit (box, sack, barrel, etc), with the weights and dimensions of each container included in the consignment.
The packing list must be prepared by the warehouse staff in charge of order preparation and reviewed by the warehouse manager before the consignment leaves the warehouse. A separate packing list must be issued for each order. Several orders can be loaded onto the same vehicle, so the driver of a vehicle might be given several packing lists.
Within the Movement, waybills are often used as packing lists, in which case there is no need to include a separate packing list.
Requisition (stock request form) | Packing list | Waybill | |
---|---|---|---|
Prepared by | Requestor | Warehouse staff (storekeeper) | Warehouse staff (dispatcher) |
Authorised by | Stock owner (budget holder) | Warehouse manager | Warehouse manager |
Received by | Warehouse staff | Transporter Consignee | Transporter Consignee |
Signatory | Warehouse staff | Storekeeper Warehouse manager | Warehouse manager Transporter Consignee |
Contents | Details of items requested and quantity (use item codes if possible) Requested delivery date and place | Detailed contents per packaging unit (box, container, pallet...) Weight and volume per packaging unit | Total number of packaging units per consignment Total weight and volume Sender and consignee details Transporter details |
Reference to | Programme code (budget, activity) | Requisition(s) | Packing list(s) |
Copies | Requestor Warehouse | Warehouse Receiver | Warehouse (x2) Receiver Transporter |
Available to download here.
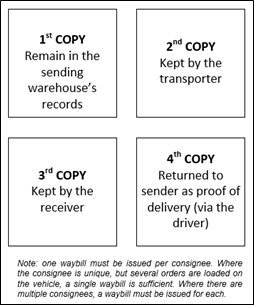
A waybill must be raised in four copies by the warehouse staff coordinating the shipping of the consignment.
It must outline the number of boxes/ pallets /containers making up the consignment and refer to the orders and/or
that have been loaded onto the vehicle – either use references or packing list references, noted on the waybill.The total number of containers and the weight and volume of the consignment for each individual order loaded onto the vehicle must be noted on the waybill.
How to prepare a consignment
The careful preparation of a consignment will avoid losses, claims and discrepancies, and mitigate the risks involved in delivering it to its consignee.
Step-by-step order preparation:
- Pick the items to be shipped and move them to the dispatch area.
- Group items into containers or onto pallets (having checked container size requirements with the consignee).
Remember to keep empty boxes/containers/pallets in the warehouse for re-packaging where required. - Split the consignment by item type – refer to the list of requirements for each item and document any dangerous goods as required.
- Count the total number of containers in the entire consignment.
- Print labels for each container, ensuring a is noted on the label if applicable.
- Safely close all containers, shrink-wrap and strap pallets.
- Stick labels to containers/pallets.
- Weigh and measure containers individually.
- Report consignment details on a packing list.
- Obtain packing list sign-off.
- Raise waybill for the consignee.
- Arrange or order transport services.
- Prepare vehicle loading plan as per agreed vehicle specifications (including box list).
- Load vehicle (ticking off boxes/pallets on the list as they are loaded) and hand documentation to the driver.
- Share the packing list, waybill and driver contact details with consignee to inform them of incoming shipment.
For details on shipping goods, see the Transport chapter.
Read the next section on Stock takes and reconciliation here.
Related resources
Download useful tools and templates